Top health and safety challenges in construction and how to manage them
Are you aware of the top health and safety challenges in the construction industry? Learn how to address them effectively.
-
Julia Boraston
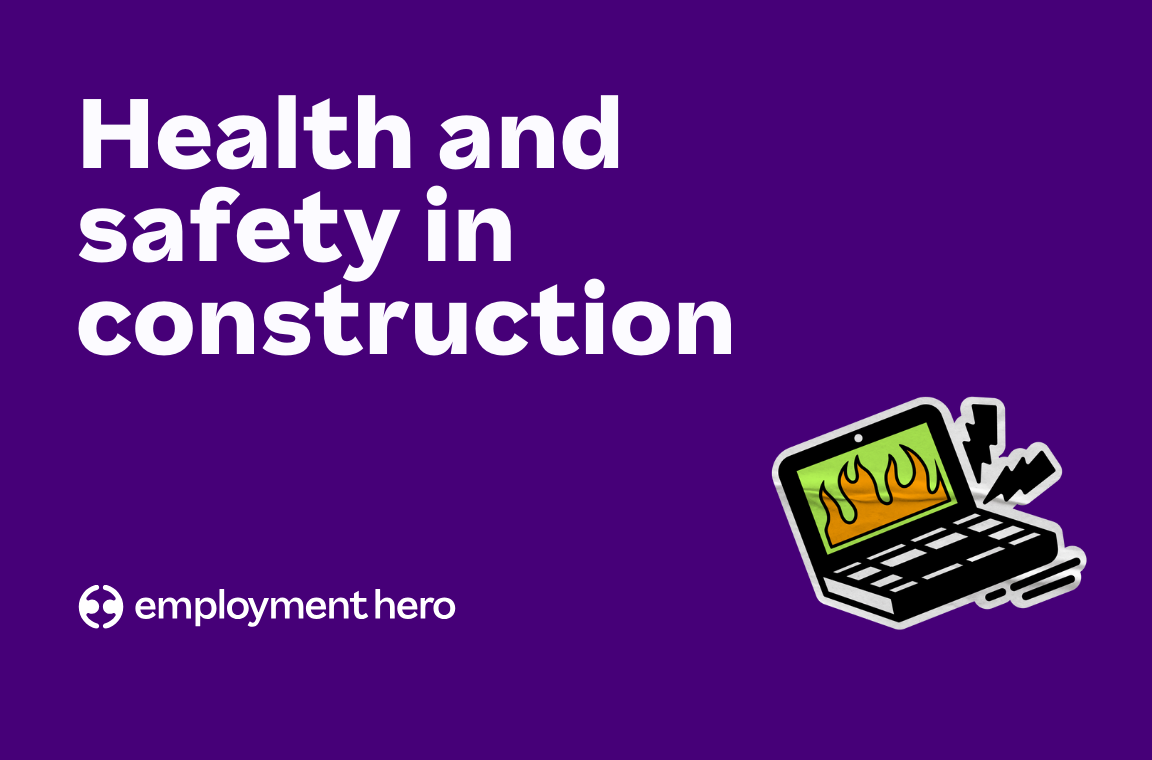
Contents
According to construction industry WorkSafe data, each year, thousands of Kiwis take more than a week off the job for a work-related injury.
If you’re an employer in the industry, you’ll know first hand that can throw a real spanner in the works, cause major delays, and put a sizable dent in your bottom line.
That’s why proactively managing health and safety challenges is crucial for NZ construction businesses.
So, what are these challenges, and how can you protect both your people, and your profits? Find out below.
Overcoming communication barriers on construction sites
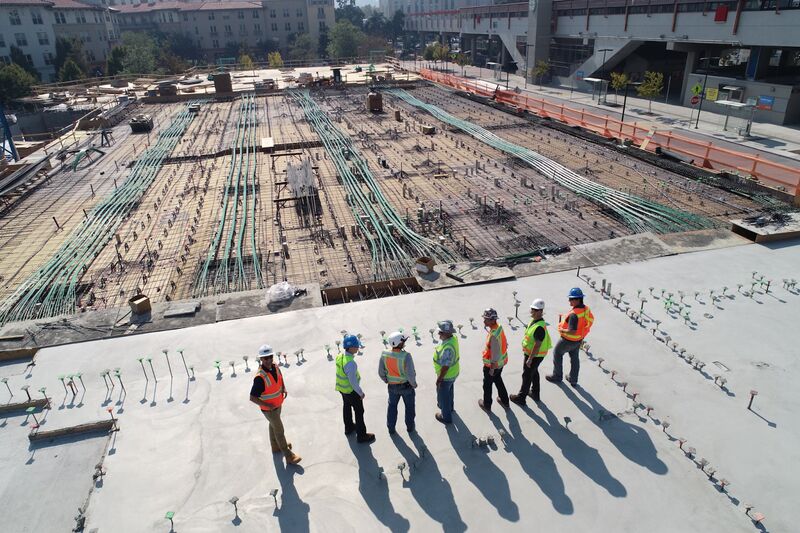
Many NZ construction projects involve hundreds of construction workers from all over the world, working across several site locations and requiring specific health and safety measures. That means communicating essential health and safety guidance to all involved can be particularly challenging.
Here’s a few tips to make communicating health and safety guidance breeze:
- Ensure you have a process in place for reporting health and safety incidents, and how to manage them as they arise.
- Give employees an easy way to communicate with you about their wellbeing at work and identify any potential hazards.
- Ensure any health and safety training is communicated clearly and accessible to all.
- Make sure all employees have read and understood your health and safety policy.
- Monitor hazards and if they change, ensure you communicate with the team and explain how they should navigate it.
- Ensure everyone has a written employment agreement stating any hazards and how to manage them.
- Make compliance reporting easy by logging any incidents in the Employment Hero platform, and downloading custom reports in just a few clicks.
Adapting to evolving WorkSafe NZ regulations
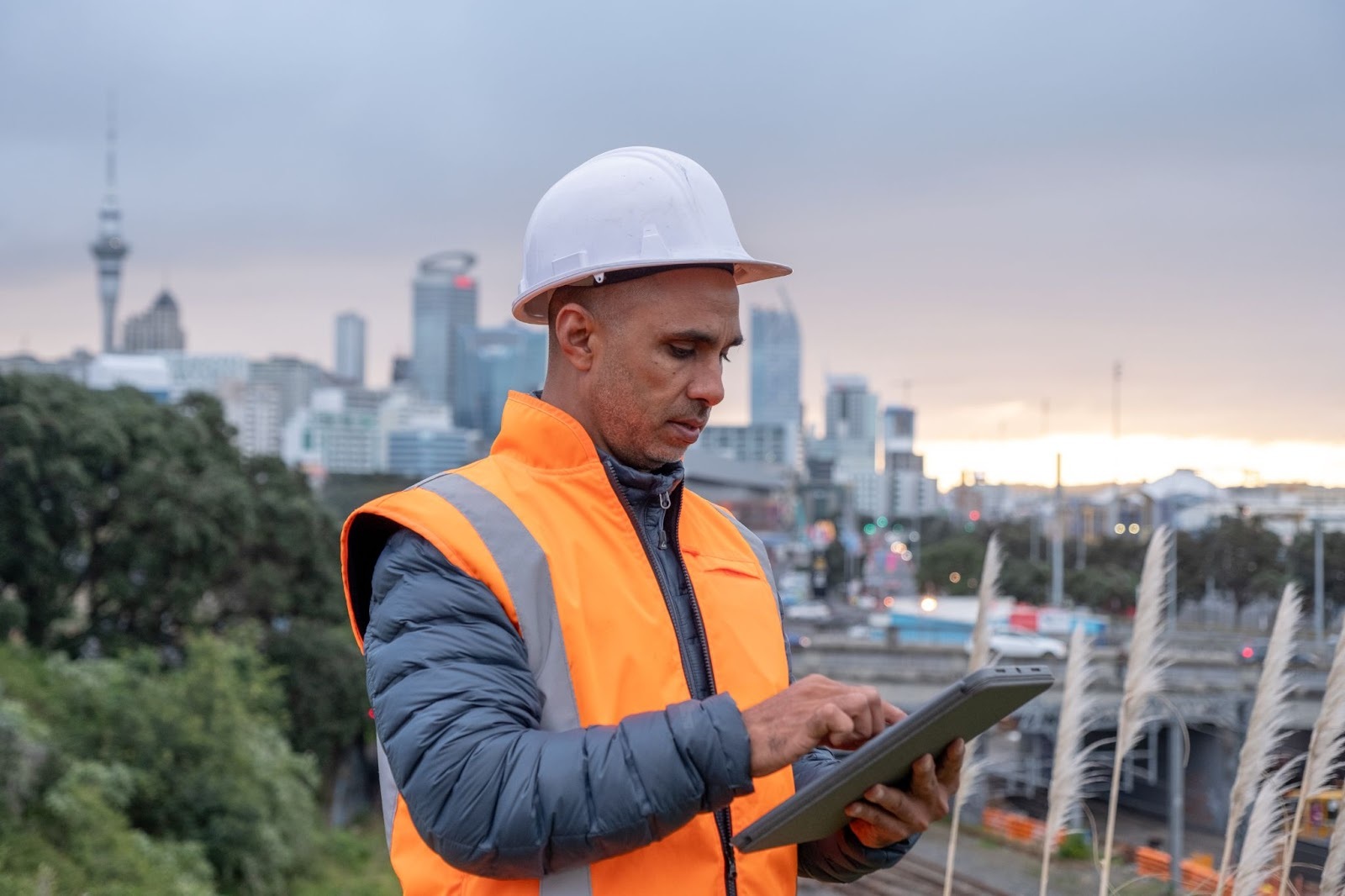
The government agency WorkSafe enforces one of the main pieces of legislation covering health and safety at work – the Health and Safety at Work Act 2015 (HSWA). WorkSafe may make changes to its policies regularly, and when you’re a busy manager or business owner, it can be hard to keep track of them.
However, failing to stay on top of workplace regulations may result in preventable injuries, time off work for key team members, and penalties.
- Ensure workplace health and safety policies are regularly reviewed and updated to ensure they reflect the current law.
- Retrain key staff members as and when regulations change.
- If you need on-demand support, ask an expert in HR and employment law.
- Subscribe to WorkSafe’s newsletter
- Regularly check the Employment Hero site for recent employment law updates
- Use employment software that can give you automatic warnings if there are changes to WorkSafe regulations, or general employment law.
Did you know?
Legally, you need to notify WorkSafe of any serious injury, illness, or incident that happens to a person or people carrying out work, or as a result of work that your business or organisation is responsible for.
Protecting your team from hazardous materials
Construction sites often involve the use of hazardous substances, such as asbestos, lead paint, or solvents. Exposure to these materials can lead to serious long-term health issues, including lung diseases or poisoning.
To reduce risks associated with hazardous materials:
- Always conduct a risk assessment before starting any work with hazardous substances.
- Provide workers with proper PPE, including respirators.
- Ensure proper ventilation when working in confined spaces where hazardous fumes can accumulate.
- Store and dispose of hazardous materials according to regulatory guidelines.
- Provide accessible training for all construction workers who will be expected to work with or around hazardous materials.
- Make sure everyone on site understands – and uses – your incident reporting system so you can stay on top of your health and safety obligations as an employer.
Hero tip: you can build custom training modules in the Employment Hero platform and assign them to team members for digital acknowledgement.
Navigating risks associated with heavy machinery
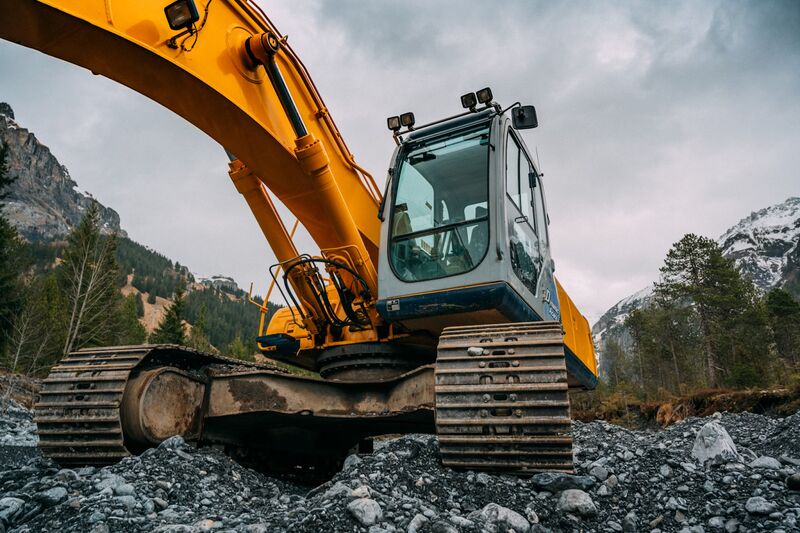
Construction sites with heavy machinery like cranes, bulldozers, forklifts and excavators are filled with health and safety risks. Accidents involving machinery can result in serious injuries, and even fatalities.
Preventive measures to reduce risks include:
- Ensuring all machinery is regularly inspected and maintained.
- Providing safety training for workers operating heavy equipment.
- Clearly marking areas where machinery is in operation to avoid accidents.
- Making sure that any risks due to machinery are outlined in your employment agreements, workplace policies, and training modules.
Ensuring safety with power tools
Construction workers can suffer from cuts, lacerations, or even more severe injuries when power tools malfunction or are used improperly. For these reasons, employers need to put preventative measures in place to protect workers – and the business.
- Train all staff on the proper, safe use of all power tools
- Regularly inspect all power tools for malfunctions, and replace when needed
- Opt for tools with safety features such as automatic shutoffs or safety guards
- Ensure any risks associated with power tools are outlined in your employment agreements, workplace policies and training modules.
Best practice health and safety tips
Provide personal protective equipment
Construction companies must provide their workers with the necessary PPE to minimise the risks they face on site. This includes helmets, safety boots, eye protection, and hearing protection, among other essentials.
In addition to providing PPE, employers must also ensure that employees are trained in its correct use and maintain the equipment to ensure it remains in good condition.
- Helmets must protect against head injuries from falling objects.
- Safety boots need to shield feet from heavy tools and debris.
- Eye protection may be needed to prevent eye injuries from flying particles or chemical splashes.
- Hearing protection reduces noise exposure from loud machinery.
Failure to provide the correct PPE can lead to severe accidents and legal consequences for construction companies. Find out more about PPE on the WorkSafe site.
Provide regular safety training
Safety training is a critical component of maintaining a safe working environment on construction sites. Workers must be equipped with the knowledge and skills to identify hazards, use equipment properly, and respond to emergencies.
Key elements of an effective safety training programme should include:
- Hazard identification: Teaching workers how to spot common hazards like slips, trips, and falls, as well as more specific risks like those associated with heavy machinery and hazardous substances.
- Emergency procedures: Workers should know how to react in case of an emergency, whether it’s a fire, equipment failure, or a medical emergency.
- Proper use of PPE: Training on how to properly wear and maintain safety gear is essential to protecting workers.
- Safety protocols: Clear guidelines on how to work safely, including when and where it’s safe to operate machinery, use power tools, or work with hazardous materials.
- Training should be ongoing, with regular updates to ensure that workers are always up to date on the latest safety standards.
For a comprehensive list of tasks, take a look at our Workplace Health and Safety Induction Checklist.
Did you know?
As well as the HSWA, employers in the construction industry are subject to the same employment laws as other industries, including the Employment Relations Act, the Holidays Act, the Minimum Wage Act and others. The nature of construction work calls for employers to pay special attention to health and safety regulations, but there’s additional compliance requirements to monitor too.
You’ll find a comprehensive HR compliance checklist for Kiwi businesses here, covering everything from recruitment to payroll and more.
Employment Hero has all the tools you need, in one place
Managing health and safety in construction can feel like a workplace hazard in its own right. Fortunately, our Employment Operating System offers all the tools you need in one sleek toolbox.
A user-friendly platform, the Employment Operating System offers customisable health and safety training modules, policy templates, an incident reporting system, and on-demand guidance through our HR Advisory service. Plus, you can manage your entire workforce from the same place – recruit with SmartMatch, onboard, digitally assign policies and training, manage leave requests, payroll and so much more.
If you’re ready for a new approach to HR, compliance and employee management, book a demo today.
Disclaimer: The information in this article is current as of 26 March 2025 and has been prepared by Employment Hero Pty Ltd (ABN 11 160 047 709) and its related bodies corporate (Employment Hero). The views expressed in this article are general information only, are provided in good faith to assist employers and their employees, and should not be relied on as professional advice. The information is based on data supplied by third parties. While such data is believed to be accurate, it has not been independently verified and no warranties are given that it is complete, accurate, up to date or fit for the purpose for which it is required. Employment Hero does not accept responsibility for any inaccuracy in such data and is not liable for any loss or damages arising either directly or indirectly as a result of reliance on, use of or inability to use any information provided in this article. You should undertake your own research and seek professional advice before making any decisions or relying on the information in this article.
Related Resources
-
How to answer salary questions in job interviews
Learn how to confidently discuss salary expectations in NZ job interviews. Use these expert tips to research, respond, and negotiate…
-
The history (and future) of the cover letter
Discover the origin and evolution of the cover letter—from Da Vinci to AI tools. Learn if cover letters are still…
-
How AI tools can streamline your job search in New Zealand
Discover the best AI tools to fast-track your job hunt—from resume building to interview prep. Learn how to work smarter…